Why should we plan for BIM for Operations?
BIM models created by professionals are a valuable source of information on building spaces, equipment and systems. Thanks to BIM for Operations, the tedious work of professionals in architecture, engineering and construction (hereafter: AEC professionals) can therefore significantly improve the entire building life cycle.
Since the operations phase of a building’s life cycle is much longer than the design and construction phases and represents 75% of the total costs incurred, the benefits of transferring the models at the end of the building projects are obvious.
In particular, it accelerates the achievement of building performance objectives in the first years of operations by:
- facilitating the location of pieces of equipment and systems in an unfamiliar building;
- providing quick access to warranty data, manufacturer’s specifications, etc.
As such, there is a hype for BIM for Operations.
Managers must be cautious, however; BIM models were not originally created for building operations. To enable them to fulfill this new function, it is necessary to establish good practices to harmonize the needs of building operators with those of professionals in architecture, engineering and construction. Ideally, this process should be initiated upstream of the design of the model. All is not lost if the process is started further down the line, though, it will only be more difficult and thus more expensive.
The purpose of this section is to provide recommendations to Property Owners, Operators, Contractors and Professionals (architecture, engineering and construction) to facilitate the use of BIM for building operations and maximize the time and effort invested in BIM models to make buildings the most cost-effective possible throughout the life cycle.
Ideally, this harmonization and standardization process should be initiated before the model is designed. If this was not done, all is not lost! However, the process will be more complex, longer and more expensive.
At Archidata, we have more than 20 years of experience in developing web-based solutions to assist property management throughout the building life cycle, from design to operations. Our solution is based on the tools used by property owners, facility managers and AEC professionals
We see the full potential of BIM for Operations, however, after five years of dealing with all the problems associated with moving to 3D models for operations at the end of projects, we can conclude that the difficulties were greatly underestimated. In this paper, we present a series of recommendations to align the requirements for operations with those of AEC professionals to make the most of BIM models and thus, the buildings. Archidata also offers its services and Solution to facilitate this transition.
Archidata can facilitate this transition and offers its support services to:
- provide guidelines/standards to the professionals who will create the models;
- recover the models at the end of the projects;
- update the models continuously;
- manage the "master model" and model parts for retrofit projects involving only portions of a building;
- standardize real estate portfolio composed of a combination of BIM model and CAD plans.
( See section on Digital Transformation )
The main topics discussed here are:
What is BIM for Operations?How do we use BIM for Operations in a practical way?
What are the benefits of BIM for Operations?
What is the problem of transferring the BIM model to owners?
What information must be added to the models to create a BIM for Operations?
What are our overall recommendations to owners/operators, contractors and professionals?
What are our technical recommendations when creating a BIM model?
What if operations requirements are not included in the as-built BIM model?
How to establish the Level of Information of equipment (LoI)?
How to keep BIM models up-to-date?
How to combine BIM models with traditional CAD drawings?
What is the Uniformat II standard?
What is the IFC format?
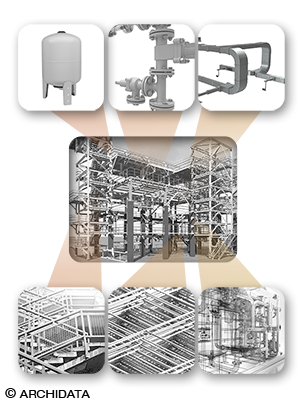
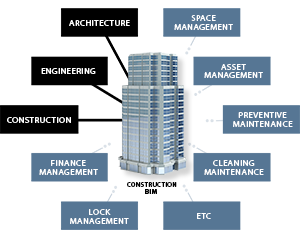
What is BIM for Operations?
Traditionally, BIM (Building Information Modeling) is an intelligent 3D-based process that provides AEC professionals with the information and tools they need to plan, design, build and manage buildings and infrastructure more effectively. [Autodesk (https://www.autodesk.com/solutions/bim)]
For AEC professionals, the advantages of BIM are twofold: working in 3D and superposing data from several disciplines. On the one hand, working in 3D allows for any modification to be automatically applied to all building floors at the same time, which is a significant advantage over working with 2D CAD drawings. 3D visualization also facilitates the work of construction professionals who benefit from a better understanding of the spaces. On the other hand, the combination of information in interactive 3D models makes it easier to detect and manage clashes.
BIM is not just a mere 3D representation of a building, it is a database grouping all characteristics of technical components. A wealth of information on architectural, structural, mechanical, electrical and plumbing components can be integrated into this database: materials, volumes, shapes, colors, fire resistance, brands, functions, maintenance, energy consumption, environmental impact, etc.
The industry quickly realized the potential of these models. By adding information levels, a BIM model becomes multidimensional: time planning (4th level or 4D), cost estimation (5th level or 5D) and energy analysis (6th level or 6D) during design and construction phases, and, finally, building operations (7th level or 7D) throughout the life cycle.
This seventh level of information, sometimes called the BIM-7D, is what interests us here.
Much of the information on spaces, equipment and systems contained in the BIM model database is required for building operations: asset maintenance, preventive maintenance, control management, space management, etc.
For BIM models to be useful for operations, one must then ensure that all the required information that AEC professionals have in hand (and that operators need!) is incorporated into the model in a standardized way. As such, this information would be understood by operators and retrieved automatically by property management (hereafter: PM) software (in IFC format). Our goal is to provide recommendations to facilitate this process.
As part of BIM for Operations, it is more realistic and productive to see a BIM model as a database that powers the different building operations PM software (space management, document management, asset management, preventive maintenance, building controls, fire protection, financial, etc.) than as a tool used for operations itself.
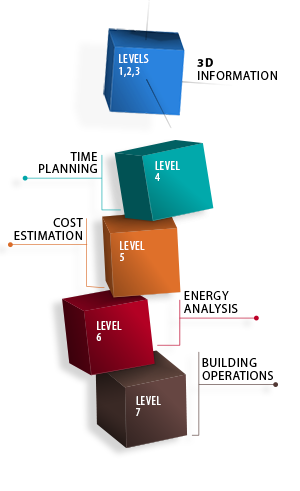
How do we use BIM for Operations in a practical way?
Different approaches are currently being developed to use BIM models as part of building operations.
One of the options considered is to bring all the information necessary for building operations into the BIM model. At first glance, there are obvious advantages to this approach since all the information is centralized and spatialized. There exists nevertheless major drawbacks resulting from BIM models being very heavy and complex to manage. As a result:
- Data entry required for BIM for Operations is very expensive since it must be done by professionals familiar with Revit.
- Consulting the model requires very powerful hardware and expensive specialized software.
- The complexity of the model also makes it very difficult to update the data, the model quickly becoming obsolete. Even in the absence of major renovations, frequent changes within a building can quickly make a model too outdated to use.
- Each professional work on their own BIM model which they occasionally combine for clash detection. There is not a single BIM model of a building; there are as many versions as there are firms participating in a project.
A BIM model is a support to design and construction and is not designed for IT management. Any attempt to impose this new function is doomed to failure in our opinion.
It is therefore very difficult to imagine that building operators would be able to consult an integrated BIM for Operations model for daily interventions and that they would be able to keep it updated.
The other option (the one we recommend) is to extract from the model information relevant for operations and to send it to PM software (for asset maintenance, preventive maintenance, health, control management, etc.). The benefits are:
- Operators will be able to use the 3D model only when they need it, saving time, money and effort.
- Updates can be done in PM software and transferred to the model when needed.
- By using proven PM software, operations do not put all their eggs in one basket.
- The data of an entire real estate portfolio can be consulted and managed centrally. Indeed, a standard BIM model only contains data for a single building.
In this case, using IFC (an industry standard) will facilitate interoperability between systems.
One can also imagine a middle of the road solution where a simplified model including only the data relevant to operations is created – in the same way that professionals have created a version of the model for their own needs for the design and construction phases.
Here, we focus on accessibility and standardization of data and have in mind the extraction of data. Although we do not advise taking this path, all of the recommendations presented here apply in the context where operations will access the data directly from the model.
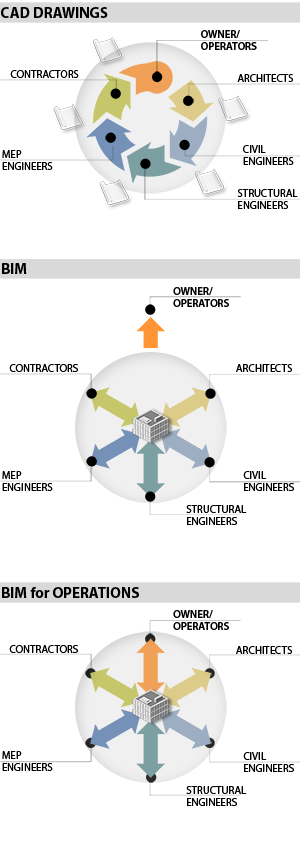
What are the benefits of BIM for Operations?
Access to a BIM model can save a lot of time for the operations team at the end of a new building or building expansion project.
If all the information on equipment that is already available and spatialized in a BIM model is transferred automatically to the building owner, this could save months of work for operators by allowing them to locate pieces of equipment in unfamiliar spaces and find useful data such as end of guarantees, technical specifications, user manuals, etc. This will increase the profitability of the building in the early years, especially as the risk of breakage and failure of equipment and systems are the highest in the first months of activity (the « blind spot » period, according to Geoff Zeiss; see below).
In an article on his blog Between the Poles - https://geospatial.blogs.com/ (Source: https://www.spar3d.com/blogs/guest-blog/bim-for-fim-big-roi/), Geoff Zeiss summarized the results of George Broadbent's first analysis of Microdesk at SPAR3D 2018 in Anaheim regarding BIM's return on investment for operations in a series of case studies (hospitals, medical research center, airport and university).
- Reduce by ≈10% the time required to train a junior operator;
- Reduce by 50% the time required to evaluate internal requests for intervention by avoiding the ordering of scans of paper plans;
- Reduce by ≈80% the costs incurred by simply searching for the information needed to maintain a piece of equipment;
- Save 5% of operating costs per year.
Since operational costs account for 75% of total building costs and accumulate over several decades, BIM for Operations significantly improves building profitability.
From our experience, another important form of ROI is a 50% to 75% decrease in data entry costs in PM software through reduced employee time and in risks associated with inconsistent data entry.
The transfer of the BIM model to the building operators makes new buildings functional and productive more quickly. For the same reasons, the BIM 3D model also facilitates the transmission of information when a building is sold.
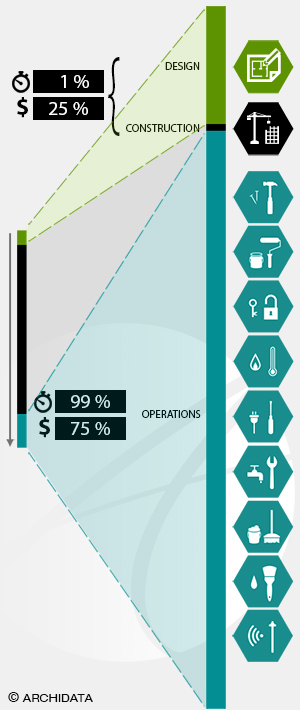
This phase is not only much longer than design and construction phases, but directly affects the well-being and productivity of a wide variety of occupants and stakeholders..
What is the problem of transferring the BIM model to the owners?
A key element to the success of BIM for Operations is to realize that the specific issues of design/construction phases are very different from those of building operations/operations-maintenance/asset management.
It is important to understand that BIM models are created for specific purposes that have little to do with building operations: facilitating collaboration between professionals during design, detecting problems (clash detection) before construction begins and facilitate management of work during construction.
Thus, the data that is included in the database associated with BIM models created by professionals is not necessarily the data that will be relevant and necessary to building operations.
Take for example the data related to equipment. The size and shape of equipment is very important during the design and construction phases to ensure there is enough space to accommodate it. While the warranty end date and the contract number in case of equipment breakdown is of little importance at the time of design; it's the opposite for operations.
Another example of differences in requirements is the spatial structure of the building. At the time of design and construction, physical spaces that are to be built are therefore often referred to in terms of phases and project areas. Spaces are assigned random codes so that professionals who collaborate on the project can find them. It is highly unlikely that premises and areas will be named, codified and numbered the same way once the building is occupied. This problem is even more difficult to manage if the codes and naming conventions are similar and overlap. For example, if the code 001 could be used both in the model and in the building without referring to the same room.
These issues may seem minor at first sight, but it can become very difficult to make the connection between the BIM model and the real building if everything is coded differently. In particular, this would prevent automatic exportation of data to PM software, depriving the owner of an obvious ROI. (See: BIM Management Benefits (ROI)).
What do we propose?
Building operators should not assume that they can simply retrieve a BIM model at the end of a project and find everything they need. Time must be invested for the model to be useful.
The sooner the effort is made to ensure that their needs are met during the design process, the less time and money will be needed in the transition. Since the building's operations phase is much longer than the design and construction phases, this constitutes a worthwhile investment).
By taking the requirements of operations into account from the start, AEC professionals can create BIM models that will increase the profitability of buildings for their entire life cycle. They will help create cost-effective and sustainable buildings.
To do this, the standardization of procedures must therefore be carefully planned by putting specialists of both BIM for design/construction and BIM for Operations at the same work table early in the BIM model creation process. This combination of expertise will establish a working method for the entire life cycle of the assets (and advise both external professional teams and in-house building operations teams).
We believe that this approach is perfectly in line with BIM's cooperative philosophy of breaking a silo effect. Getting in the habit of taking the entire life cycle of buildings from the very beginning of the design process into account should develop fairly quickly in the field – as long as good practices are developed.
Archidata and its partners can act as consultants for this transition. In the following three sections, specific recommendations are presented to achieve these goals:
- Recommendations clarifying the overall objectives to be achieved;
- Technical recommendations to integrate the needs of operations when creating BIM models;
- Guidelines for making BIM models useful for operations if a harmonization effort has not been done upstream.
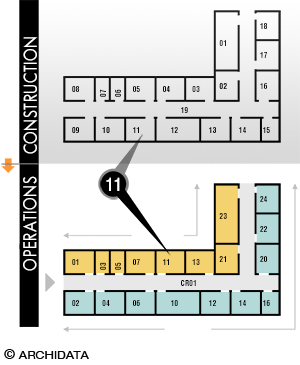
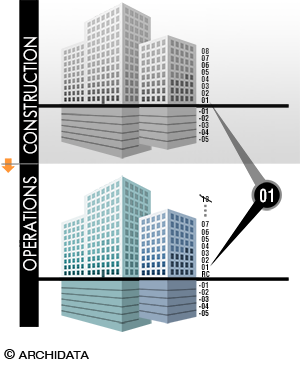
What information must be added to models to create a BIM for Operations?
It seems useless and quite impossible to ask AEC professionals to include all the information that could potentially be relevant to manage a piece of equipment at some point during the building’s life cycle in a BIM model. Not only would this burden the model with unnecessary information, but it could result in significant costs in AEC professional fees. Nevertheless, it is beneficial to ask them to integrate the basic information needed for operations so that the operations team can quickly take control of a new building. For other information, depending on requirements and budgets, the task of searching for information in manuals and integrating them into the BIM model database could be given to in-house staff rather than to an outside firm.
For most of the information, it is sufficient to have quick access to documentation related to the equipment: installation guide, specification sheets, contracts and warranties, etc.
Essential data that must be in the model should allow to:
- Locate a piece of equipment;
- Identify the system/network to which it is linked;
- Access documentation;
- Access information on warranties.
Spatialization and network connection information is usually provided in the BIM as-built model. To ensure information is optimally integrated, see the recommendations in the following sections.
Documentation is not directly linked to the BIM model and must thus be transferred separately to the owner. To ensure that all relevant documents are associated with the equipment in a model, the nomenclature used to code the information must be standardized. See our recommendations below.
From an operations perspective, the most important information that should be included in a BIM model by AEC professionals is not about technical specifications, dimensions and materials, but rather information that will help plan the maintenance of equipment: dates of purchase, installation and start-up, as well as end dates of the warranties offered by the company, by the manufacturer and by law. However, this level of information is not always necessary.
In some cases, other information such as the manufacturer's specifications, is also useful for operations. If project owners and building operators are involved earlier in the model creation process, they can along with the professional, identify what information should be modeled by the different trades. The relevance of this effort can be justified by comparing the fees proposed by professionals and those associated with data entry into internal PM software.
To better establish what information is required, we use the Level of Information (LoI) concept. All the details to help with this decision are presented below.
What are our overall recommendations to owners/operators, contractors and professionals?
Here we list some key points to remember from our recommendations; detailed and technical recommendations on the methods to be used are presented in the next section.
The key points to remember are:
BIM allows and encourages cooperation between professionals; it would be ideal to take advantage of this by involving operations teams with AEC professionals so that needs are well understood and taken into account when BIM models are created during design and construction phases. It is up to owners and building operators to be ready for these consultations and to have a list of requirements ready. This approach can be done with or without the help of experts such as Archidata.
The general goal is to develop a method that will allow, at the end of the project, to find or extract data needed for operations from the BIM model. There are practically as many ways to create BIM models as there are AEC professionals, so it is beneficial to do some standardization work to ensure that the data during both the construction and the operations phases is compatible. In particular, it is imperative to standardize the nomenclature and coding used for (1) rooms and door numbers, which are at the heart of any building operations system, as for (2) equipment to be managed and maintained and (3) for networks/systems to which they are connected.
As part of BIM for Operations, it is more realistic and productive to consider a BIM model as a database that feeds the different PM software (space management, documents, asset management, preventive maintenance, building controls, fire protection, cleaning maintenance, financial, etc.) rather than as a tool used for operations in itself.
The BIM for Operations must be part of a global vision: interoperability between systems must be considered to ensure that databases can be linked. One must (1) establish which elements of the model must be monitored and managed by the operations team, and for each of them, (2) what is the relevant data required for management and (3) to which PM software the data will be sent to.
Whenever possible, data transfer from the BIM model to PM software should be automated to minimize manual data entry by operations teams and to save time and reduce the risk of errors.
BIM models can hold a lot of information and become very heavy. Rather than requiring professionals to put all the available equipment information in a BIM model, it may be more sensible to think of what level of information (or LoI) is required for each type of equipment or system early in the process.
BIM for Operations requires to address the issue of document management. Each equipment or object embedded in a model is linked to essential documentation for operations. For operators to have a quick and easy access, the nomenclature/coding used must be the same as the ones used in the BIM model.
An important aspect in developing a BIM for Operations management plan is updating the model. Indeed, buildings are constantly evolving and the model has to be an accurate representation of the building and a reliable source of information. The creation of a workflow and a procedure for updates that takes into account design, construction and operations needs will allow a smooth transition between projects and operations
Finally, there is the issue of data standardization between BIM models and traditional CAD drawings. Depending on the identification of needs, it may be decided to create BIM models for the entire portfolio at once or to manage the transition gradually. In any case, a global action plan will have to be developed.
What are our technical recommendations when creating the BIM model?
Here is a list of five main recommendations drawn from our own experience when a BIMBuilding Information Modelingmodel is recovered at the end of a construction project. Please note that these recommendations are based on the Revit software usage but that the same principles can be applied to other softwares.
In short, here are the 5 main recommendations:
Below, we will elaborate on each of these recommendations..
To ensure that the data and documents required for operations are incorporated into the model in a standardized manner, it is the responsibility of owners or building operators to (i) provide the necessary documentation and guidance to the professionals so that they can meet their requirements and (ii) monitor regularly to ensure that these guidelines are being followed.
1. Spatial Structure Codifing
The nomenclature used to refer to sites, buildings, wings and floors is very important for operations because it is the basis of several search engines for PM software and is essential for signage in a new building.
For construction, it may be practical to identify physical parts of the wing, building or site in the model according to areas and phases of projects. It is also customary to number plans with a temporary construction number to help understand the site. However, these areas and numbers will not be useful once the project is finished.
The identification of the rooms with the final and official names and signage is essential in the model because preventive management use this nomenclature to locate equipment and for work orders. This is one of the many ways to make BIM models useful to humans.
- If the information provided in the BIM model that is intended to describe the building's spatial structure “as-built” does not match the signage used in the building, this may be detrimental to data transfer.
- If the codes used to describe construction-relevant spaces and those relevant to operations are well differentiated and standardized, it will be easy to delete or ignore the information that is not relevant to operations when transferring data at the end of the project.
Our recommendations are as follows:
2. Differentiation between rooms and other types of space inside buildings
We noticed that in BIM models created with Revit the same notion of “space” is used to describe concepts that should be clearly differentiated for efficient building operations:
- administrative units (for example, the different departments of a hospital or the departments of a university);
- rooms (offices, washrooms, stairs, etc.);
- workstations within a room (spaces in a laboratory, office within an open space);
- spaces reserved for specialized equipment.
Since spatialization is at the core of building operations, a poor distinction of rooms among other types of space can impair the ability to locate pieces of equipment and work orders. The large amount of work that is then required to readjust the BIM model to make it fit with reality is sometimes enough for building operators to abandon BIM for Operations altogether. This is exactly what we want to avoid!
Our recommendations are as follows:
3. Standardization of codes and definitions of room usages
The code for room usage and its definition are important for operations since spaces with different usages do not contain the same equipment and systems and do not all require the same type and frequency of maintenance.
Since this will be an important issue starting at the planning phase for the rooms, it is important that the proper level of information on rooms be provided in the models. As early as possible in the process, building operators must provide a standardized list of codes for rooms and, if relevant, occupancy and workstations.
Our recommendations are:
4. Standardization of information on pieces of equipment and systems
It is important to understand that each professional can develop its own library of BIM objects. Thus, equipment and system codes used by architects and engineers may vary from one firm to another and can thus lead to a lack of homogeneity within the same project. From our experience, it can be very difficult, if not impossible, to assess the function or nature of equipment from some of these codes.
We therefore recommend doing a standardization exercise for equipment to be managed (there is no need to burden the BIM model and the work of professionals for other types of object).
Our recommendations are as follows:
For automated data sharing, Archidata recommends that data be transferred to other systems in order to avoid as much manual data entry by planning and operations teams as possible. These systems include, but are not limited to software for
- space and document management
- asset and preventative maintenance,
- building control management,
- fire prevention management,
- maintenance,
- cleaning services,
- locks,
- finances,
- etc.
5. Document Management associated to equipment
Much of equipment related information does not need to be included directly in the mode, as long as operators have access to all documentation. This documentation is essential to building operators; they will benefit greatly from having it linked to the model and accessible at the end of the project.
Our recommendation is:
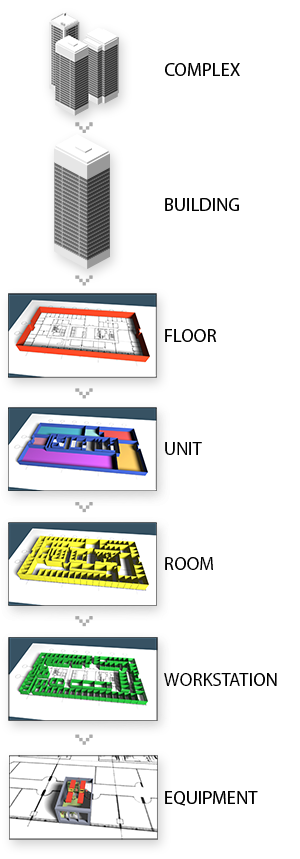
What if operations requirements are not included in the as-built BIM model?
If the above recommended information required for BIM-Operations is not included, all is not lost! It is still possible to take advantage of the modeling done by professionals to facilitate the transition from construction to operations.
One option is to ask AEC professionals to modify the as-built BIM model such as to include the required data. In our experience, this involves paying the fees of qualified specialists and could be very expensive.
Another, less expensiveoption is to create a matrix of correspondence with the professionals between the coding used internally and that used in the model. This would apply to areas, equipment and systems. It will then be possible to automatically modify the data extracted from the BIM model so that it is compatible with the coding used by PM software of the different operations services.
Archidata offers a conversion service to help its customers when they get a BIM TQC model that has not been harmonized with their needs.
How to establish the Level of Information of equipment (LoI)?
The BIM model and 3D modeling introduce the concept of Level of Detail (LoD) which is used to determine the level of precision required when modeling a piece of equipment or a surface. As mentioned before, for operations, the exact shape of a piece of equipment and even its size does not matter, while data on the manufacturer, the warranty, etc. is essential. Thus, in the context of BIM for Operations, we rather use the concept of Level of Information (LoI).
The required LoI can vary greatly from one device to another: data required to manage a soap dispenser in bathrooms is probably less than the amount required to manage a generator or CT scan. It is important to consider all building operations services when establishing the LoI: it may be that less detailed information is needed for one type of equipment (for example, tools to keep the environment clean) than for another (for example, preventive maintenance or control management.
It is quite possible that a great deal of detail on dimensions, shape and positioning is required to plan for the required space and connections to equipment networks during the design and construction phase, but that minimal information is required for management it in the context of operations. This is the case, for example, for most architectural elements (e.g. columns, windows, stairs). Another example would be common equipment connected to pipes, valves and ducts inside walls (e.g. isolation valve, etc.) that are complex to install on site, but for which only information, on the adjoining room they are in and the network they are connected to is useful for operations.
On the other hand, it is possible that an easy-to-install equipment needing little modeling detail during design and construction requires a detailed level of information for operations. For example, this is the case for an electrical panel that requires little modeling because it is connected to a network outside the walls, but for which detailed information is required for operations because it is crucial to the proper functioning of the building. Another example would be expensive, mobile, specialized equipment such as some lab equipment purchased once construction is complete and for which only the footprint and volume have been modeled for construction but for which high levels of information are required for operations.
Close correspondence between LoD and LoI is nevertheless possible. For example, a soap dispenser requires minimal levels for both LoD and LoI, while fixed specialized equipment (e.g. medical equipment) installed during the construction phase requires high levels for both LoD and LoI.
We also drew on the tool “Kit BIM Exploitation” created by our research partners from the CSTB (French government's Scientific and Technical Building Center) which has already worked on the concept of information levels of equipment for other purposes.
We propose the following levels:
No information is transferred
In some cases, equipment can simply be ignored. The LoI 0 level could apply for example to pipes and valves that do not need to be entered into a PM software to be tracked.
Nomenclature for inventory
This level only retrieves information on the equipment's nomenclature and quantity. This level of LoI is sufficient if the only information one wishes to retain from the BIM model is equipment inventory type information at the building or site level as a whole.
Location for intervention
This additional information makes it possible to locate equipment in a space which can be done at different levels of detail according to operations’ requirements: building, floor, room, network. It is useful if each of the objects need to be located individually or if an inventory has to be done by sector. For example, all types of lighting fixtures present in a room or types of water source (drinking troughs, sink, sinks, eyewash) on a floor. LoI 2 also makes it possible to quickly identify the network to which a piece of equipment is linked and quickly cut the source before intervening.Manufacturer for document management
This additional level of detail is necessary if operators want to be able to consult information provided by the manufacturer, such as the technical data sheet of the equipment. This level is sufficient when only data sheets are necessary for the maintenance of non-specialized equipment, which could be the case of washbasins, for instance.
Installation and planning
This extra level is useful for equipment that requires regular and detailed monitoring, such as specialized equipment. One can think of information such as the date of installation, serial number, etc.
Specifications
The information of this last level is only necessary for a handful of extremely specialized equipment for which technical specifications are an important search or analysis criteria. It is not necessary or wise to include all equipment specifications with the BIM model. Required specifications will differ by equipment type and will need to be established upstream.
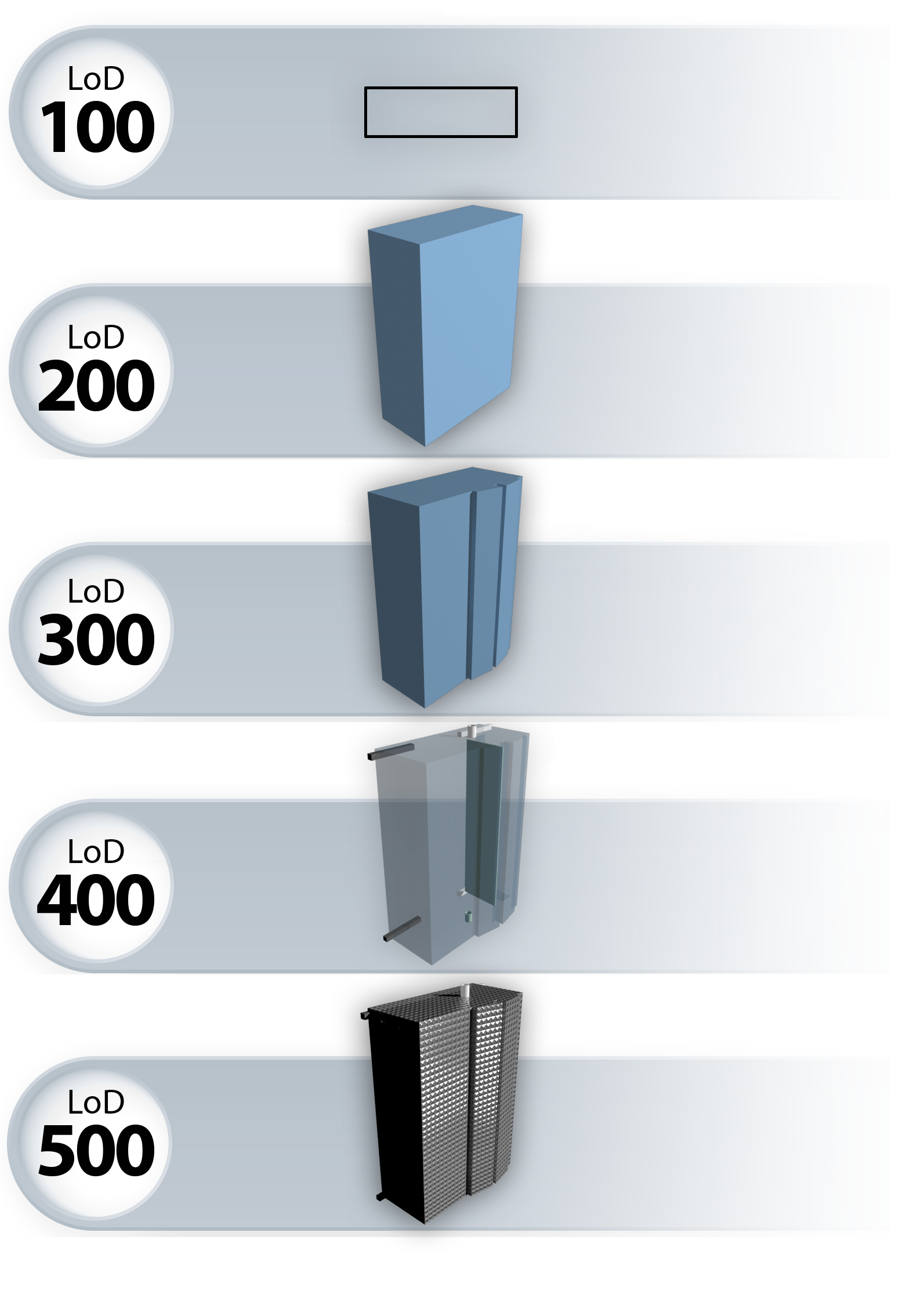
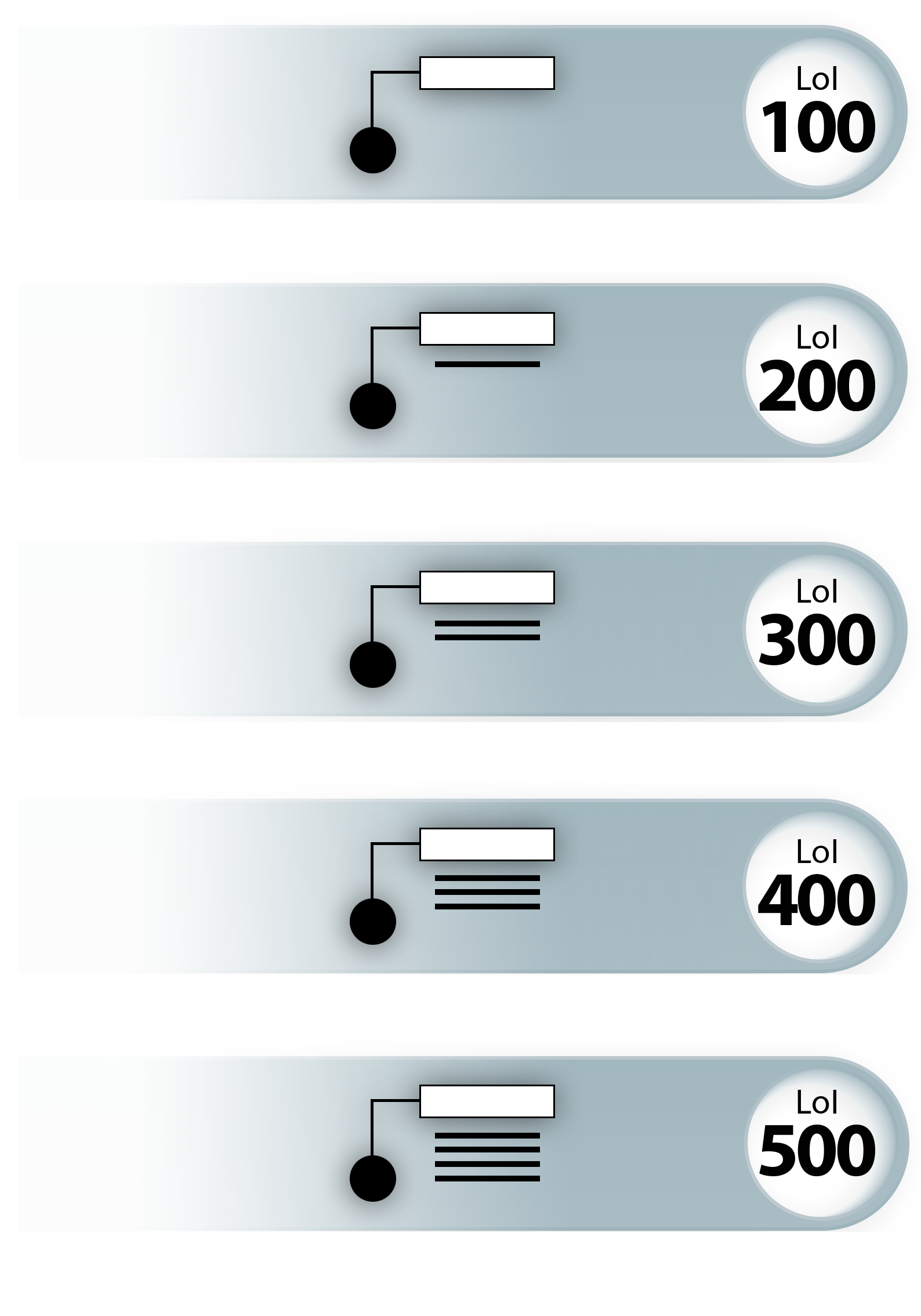
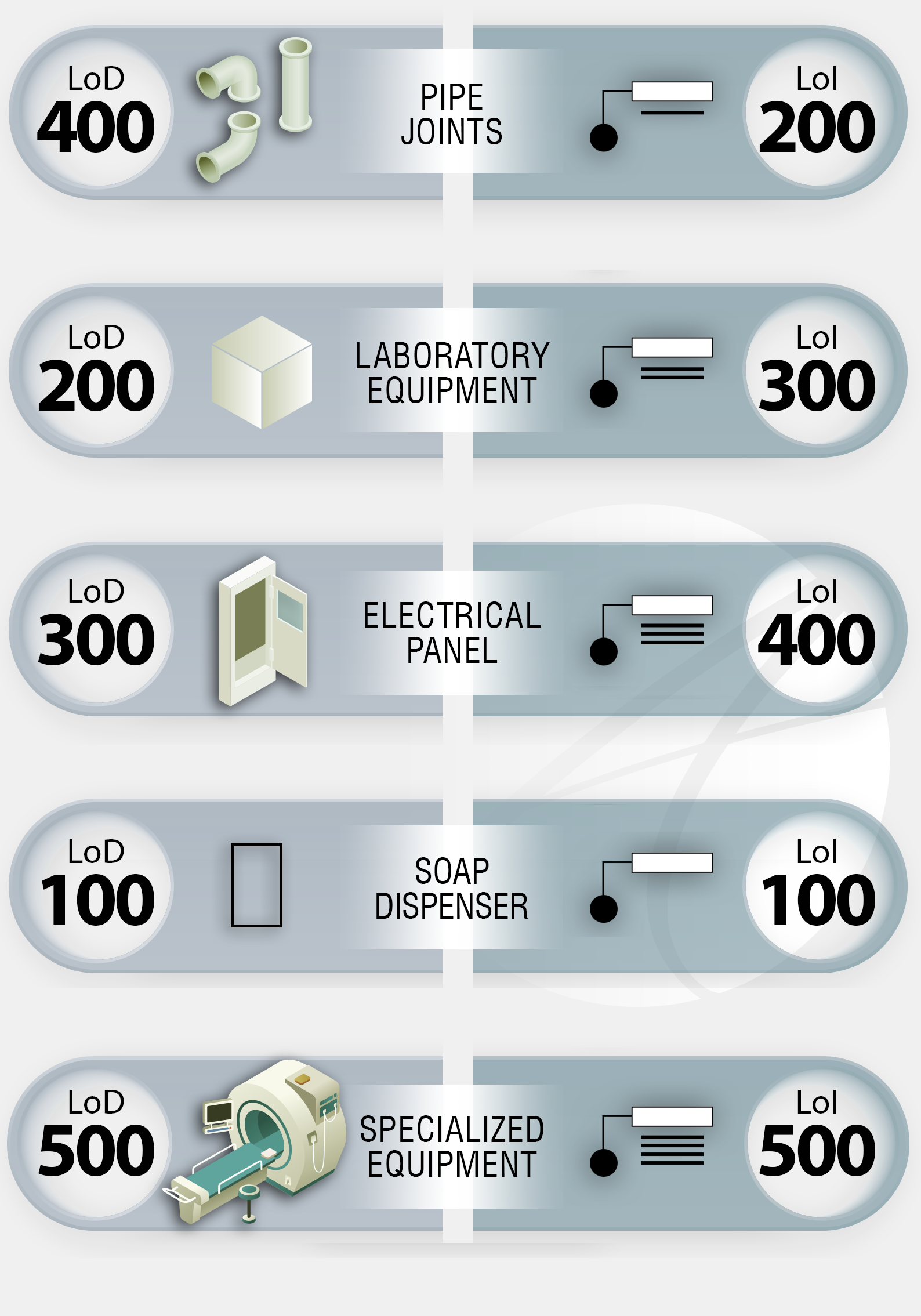
How to keep BIM models up-to-date?
One of the problems inherent to the recovery of material (whether plans/drawings/models) produced by professionals for operations is the update of information. “As built” documents quickly become obsolete not only because of projects carried out by internal and external teams, but also because of day-to-day internal operations that bring many small changes quickly accumulate: adding or removing walls, replacing equipment, remodeling and moving, changing usage, and so on.
Building operators sometimes appear to rely on the fact that professionals will update the equipment information at the time of a renovation project. They do not realize that:
- Only parts of the building that are affected by the project will be updated;
- Parts of the building not affected by the project will continue to be modified internally for the duration of the project but may not be updated by professionals;
- Several projects affecting different parts of a building may overlap in time and space making updates even more difficult.
To solve this problem, the best solution is to keep an up-to-date master floor plan. The information is updated as changes are made internally. When a new project takes place, portions of plans needed by professionals are transferred to them. The rest of the plan continues to be updated in parallel over the course of the project and the renovated portion is reintegrated at the end.
It would be a mistake to believe that BIM solves this problem. On the contrary, using of BIM models for operations increases the problems!
As the BIM model becomes the source of information for PM software databases, assuming that the BIM model provided by professionals at the end of a retrofit project is up-to-date, major problems could occur. For example, by linking the new BIM model provided at the end of a project, parts that were updated during the project would be overwritten by the outdated data model.
It is therefore important for building operators to create workflows in order to manage the update process continuously so that the model remains a reliable source of information. Archidata can help set up these workflows as well as assist in updating models.
How to combine BIM models with traditional CAD drawings?
BIM projects are just beginning to emerge for new constructions and major renovations. This often means that our clients face the problems that they have to handle a combination of BIM models and CAD drawings. There are three typical cases in which such combinations occur:
- A new building is built as part of a site containing many other buildings with CAD information;
- The owner of a large real estate portfolio acquires a newly constructed building;
- A part (wing, floor) of a large building undergoes major renovations.
In the specific context of BIM for Operations, this means that the sources of data for PM software are diverse which complicates things a little bit. It is also a problem when updating equipment for AEC when large development projects take place.
Depending on the identification of requirements, it may be decided to create BIM models for the entire portfolio at once or to manage the transition gradually. In all cases, a global action plan should be developed. Archidata’s expertise can accompany you in this transition.
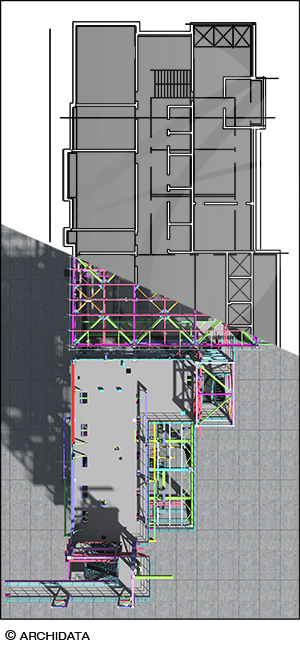
What is Uniformat II?
The Uniformat II standard is a method of classifying the elements of a building on the basis of their functions, regardless of the materials and methods used to produce them. It has been developed by a consortium of industry and governments experts and is accepted as standard by the American Society for Testing Materials (ASTM). Uniformat II makes it possible to create inventories of all categories of equipment in a standardized way in order to facilitate the transfer of information between work teams.
Uniformat's approach is ideal for developing Building Information Modeling (BIM) models because its organization allows objects to be placed in the model before their properties have been defined. It also facilitates the transfer of information between work teams and operations by allowing the classification of information even when there is an inconsistency between the coding and the nomenclature used.
Note that the Uniformat II standard was used as the basis for Table 21 - OmniClass Elements.
Uniformat II has four levels, as follows:
Level 1 - Elements of the major group, identified by a capital letter (e.g. Services, D)
Level 2 - Group elements, identified by two numbers (e.g. Plumbing, D20)
Level 3 - Individual items, identified by two numbers (e.g. plumbing fixtures, D2010),
Level 4 - Sub-elements, identified by a number or letter (e.g. Sink, D2013).
Here are the main categories of Levels 1 and 2 that are useful for building operations - to get more details, see https://www.csiresources.org/practice/standards/uniformat ou http://quebec.csc-dcc.ca/Document+Store/UniFormat/.
A - Sub-structures
A10 FoundationsA20 Basement Construction
B - Shell
B10 SuperstructureB20 Exterior Enclosure
B30 Roofing
C - Interiors
C10 Interior ConstructionC20 Stairs
C30 Interior Finishes
D - Services
D10 ConveyingD20 Plumbing
D30 HVAC
D40 Fire Protection
D50 Electrical
E - Equipment and Furnishings
E10 EquipmentE20 Furnishings
http://www.assetinsights.net/Glossary/G_Uniformat_II.html
https://en.wikipedia.org/wiki/Uniformat
http://quebec.csc-dcc.ca/Document+Store/UniFormat/
https://www.csiresources.org/practice/standards/uniformat
http://www.iceline.com/estref/popular_conversion_files/construct_code/uniformatA.html
What is the IFC format?
Industry Foundation Classes (IFC) is a free, open file format that supports an OpenBIM and was created by buildingSMART. This format is used to transfer BIM model information in a lightweight text format that can be read by different programs. The latest version as of March 2013 is IFC4.
Archidata recommends going through the IFC format for exporting data to third-party software. Indeed, this format makes it possible to export not only graphic elements, but also their associated data. Note that not all IFC entities are important for extracting alphanumeric data. As a reference, here is the list of entities that are processed. This list may change from one project to another depending on the progress that will be made in future versions of Revit.
Entities common to the spatial structure
ifcProject | Project description |
---|---|
ifcSite | Site(s) description |
ifcBuilding | Building description |
ifcBuildingStorey | Floor description |
ifcSpace | Room description |
ifcZone | Description other types of space |
Entities common to equipment
ifcFlowTerminal | Equipment powered at the end of a network |
---|---|
ifcFlowController | Control equipment of a network |
ifcDistributionControlElement | Alarm type equipment |
ifcBuildingElementProxy | Bulk equipment |
ifcFurnishingElement | Bulk equipment |
Entities common to networks
ifcSystem | Network |
---|
At the moment, the extraction of BIM models in IFC format is not perfect and a lot of equipment information is extracted under the ifcBuildingElementProxy, a category "in bulk" which does not allow for identification or classification. Until the extraction process is improved, it is important that AEC professionals include Uniformat II codes to facilitate the interpretation of models by third parties.
http://www.buildingsmart-tech.org/ifc/
https://bimbtp.com/conception/quest-ce-que-le-format-ifc/
https://fr.wikipedia.org/wiki/Industry_Foundation_Classes
http://www.objectif-bim.com/index.php/openbim/format-ifc
Ali Motamedi et al. – FM-BIM Preparation Method and Quality Assessment Measures:
www.researchgate.net/publication/325905180_FM-BIM_Preparation_Method_and_Quality_Assessment_Measures
Asset Insights – ASTM Uniformat II :
www.assetinsights.net/Glossary/G_Uniformat_II.html
Autodesk – Building Information Modeling :
https://www.autodesk.com/solutions/bim
Biblius – BIM dimensions 3D, 4D, 5D, 6D, 7D BIM explained :
biblus.accasoftware.com/en/bim-dimensions-3d-4d-5d-6d-7d-bim-explained/
BIM & BTP – Qu’est-ce que le format IFC :
bimbtp.com/conception/quest-ce-que-le-format-ifc/
Building Smart – Industry Foundation Classes :
https://technical.buildingsmart.org/standards/ifc/
Cégep Limoilou : Coordination de maquettes numériques BIM : www.cegeplimoilou.ca/formations/attestations-d-etudes-collegiales-aec/eec3a-coordination-de-maquettes-numeriques-bim/
CSI, Building Knowledge Improving Project Delivery – Uniformat :
www.csiresources.org/practice/standards/uniformat
Wikipedia – Uniformat :
en.wikipedia.org/wiki/Uniformat
Wikipedia – Industry Foundation Classes:
fr.wikipedia.org/wiki/Industry_Foundation_Classes
RIB, Estimator’s reference – Uniformat :
www.iceline.com/estref/popular_conversion_files/construct_code/uniformat.html
Linkedin, Hani Elsafadi – BIM 3D to 7D Implementation:
www.linkedin.com/pulse/bim-3d-7d-implementation-hani-elsafadi/
Objectif BIM – Le Format IFC :
www.objectif-bim.com/index.php/openbim/format-ifc
CSC, Québec Chapter – Uniformat :
quebec.csc-dcc.ca/Document+Store/UniFormat/
Spar3D, Geoff Zeiss – Does BIM really benefit facility operations? Hard data says yes:
www.spar3d.com/blogs/guest-blog/bim-for-fim-big-roi/
UK Construction Online – The Value of BIM Handover and Maintenance :
www.ukconstructionmedia.co.uk/news/bim-handover-maintenance/